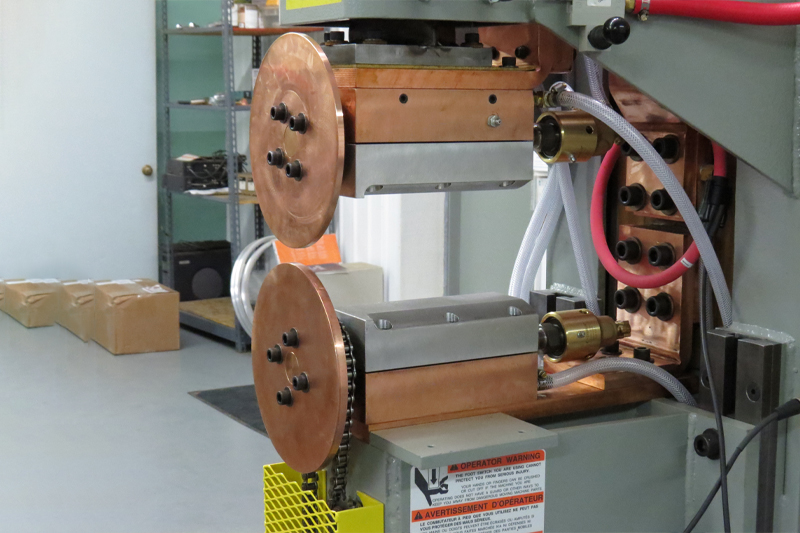
Spot and Seam Welding Machine
Spot Welding process involves welding two or more metal sheets together by applying pressure and a localized electric current. The current creates a small molten pool at the contact point, which solidifies to form a weld nugget. Spot welding is ideal for joining overlapping metal sheets in automotive and heavy machinery industries.
Seam Welding technique is used for continuous welding along a seam or edge. It involves rotating electrodes that press and pass a current along the seam, creating a continuous weld. Seam welding is often used for producing airtight or watertight seams in products like tanks and containers.
- Strong Joints: Provides robust and reliable welds that meet industry standards for strength and durability.
- Improved Productivity: High-speed operation and automation reduce labor costs and increase production rates.
- Versatile Applications: Suitable for various industries and products, including automotive parts, electronic assemblies, and metal enclosures.
- Consistent Quality: Advanced control systems ensure uniform weld quality and reduce the risk of defects.
- High Precision: Ensures accurate and consistent welds with minimal distortion, crucial for high-quality manufacturing and assembly.
- Versatility: Capable of performing both spot and seam welding, making it suitable for a wide range of applications and materials.
- Durability: Constructed with high-quality components to withstand the demands of continuous operation and deliver reliable performance.
- Efficiency: Optimized for fast operation and minimal waste, contributing to cost savings and improved production efficiency.
- Ease of Use: Features intuitive controls and settings, allowing operators to easily adjust parameters and perform maintenance.